Table Of Content
Employees should be trained on proper handling procedures as well as safety protocols such as the use of protective gear or specialized storage containers. You should also check for any areas of your warehouse that are particularly prone to damage from moisture or other elements. This is a factor most warehouse managers don’t consider, but the temperature and humidity levels in your warehouse can have a significant impact on your inventory. By installing the right security measures, you can ensure that your warehouse is well-protected and any stolen items can be quickly identified. This method can help save time and minimize errors by allowing workers to pick items from multiple zones at once.
Shift start times
This may involve adjusting shelf heights, selecting appropriate racking systems, and ensuring compatibility with material handling equipment. The movement of products between the receiving and shipping areas is easy, and the parallel positioning of inbound and outbound loading minimises bottlenecks. Across all ShipBob warehouses, the warehouse layout is centered around efficiency, accuracy, and consistency. Our warehouse setup ensures that items can be located and pick efficiently to improve order accuracy while speeding up the fulfillment process. The U shape is utilised to divide and simplify the main traffic flow in warehouses. To prevent bottlenecks, keep the entering and departing materials on opposite sides of the operation.
Perkins&Will renovates a warehouse into office space for Innolabs - The Architect's Newspaper
Perkins&Will renovates a warehouse into office space for Innolabs.
Posted: Wed, 25 Oct 2023 07:00:00 GMT [source]
Orchestrating the Symphony: Advantages of Automation Integration
You should allocate a specific area of your warehouse for storing hazardous materials and make sure that it is clearly marked. You could also use color-coded labels to indicate the shelf life of products and expiration dates. This allows employees to easily identify items that need to be moved or discarded. For example, you could assign a specific color for each type of product or use colors to differentiate between items of different sizes, shapes, or weights. Zone picking is a type of order fulfillment system in which the warehouse is divided into several different zones. Lines are used to mark aisles and guide forklift drivers while arrows and crossroads can help direct traffic flow.
Aisle layout planning
Record specifications such as dimensions, weight, and any special storage considerations. Leverage technology, such as barcode scanners or RFID systems, to streamline this data collection process. With every new warehouse layout, we recommend capturing the space for a digital twin. This new virtual version of your layout can more comprehensively communicate design changes and how they’ll impact workers than a simple photo or video.
Have a supplier engagement plan
By keeping incoming and outgoing shipments apart, the U shape also helps avoid bottlenecks. We stand by the quality of our products, and offer free consultations to determine what clients need to expand. As an eCommerce business owner, you're likely familiar with the concept of a loading dock. Additionally, employees should be trained in basic first aid and safety procedures. It is important to create SOPs for each department or role within the warehouse so that everyone knows what is expected of them and how to do their job correctly. It can also help you to identify any areas of improvement, allowing you to make changes quickly and efficiently.
Step 7: Integration of Technology
Along with optimizing storage costs, you don’t have to worry about hiring staff to manage demand, design, and optimize picking workflows, or worry about investing in technology and equipment. Your picking team will understand your current warehouse layout better than anyone because they’re constantly moving around the entire space. Be sure to work with them to identify opportunities to create better fulfillment workflows that eliminates headaches, confusion, and human error during the entire process. Once you find the right warehouse, planning and designing the layout is a crucial first step as it will impact supply chain efficiency.
Challenges of warehouse layout design
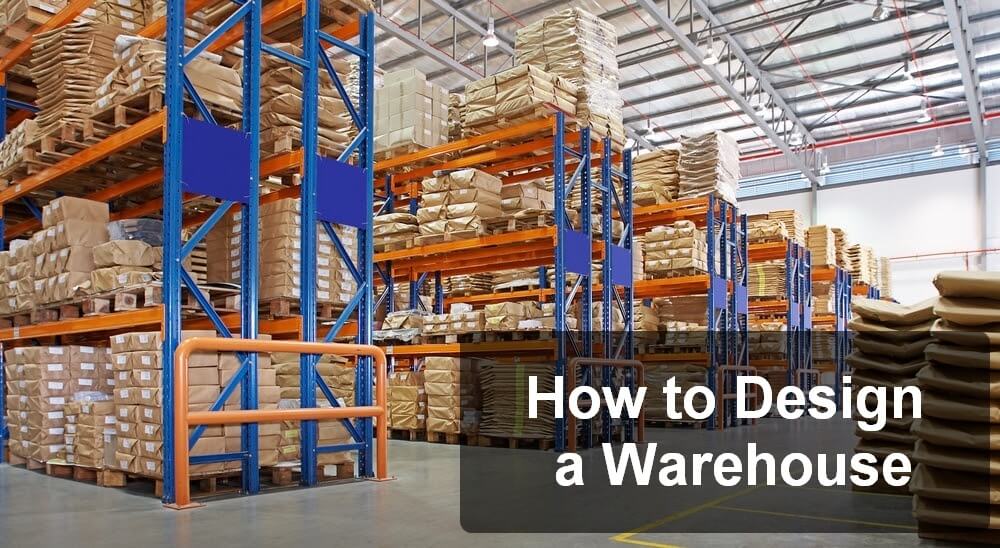
From improving space utilization to dispatching incoming customer orders quickly, this cost efficient solution can boost operational efficiency in numerous ways. An optimized warehouse layout design can also help improve customer service by reducing the time it takes to fulfill orders. Every company wants to improve productivity and speed up order fulfillment without sacrificing quality. The right warehouse layout design aims to optimize operations while reducing the chances of bottlenecks or errors. As we navigate through the intricate steps of warehouse design, Step 9 takes center stage – Flexibility for Future Changes. In the ever-evolving landscape of logistics, designing a warehouse layout with adaptability in mind becomes imperative.
Of companies are already taking automated warehouse systems very seriously and making plans to implement. All are helpful in their own ways, and finding the right fit comes down to which one works with what you currently have and hope to achieve. These automated devices traverse storage lanes, effortlessly transporting pallets to their designated locations. The beauty of pallet shuttles lies in their ability to operate within high-density storage configurations, optimizing pallet storage and retrieval with speed and precision. Explore the realm of predictive analytics to anticipate future challenges and opportunities. Implement algorithms and models that forecast potential issues within the current layout, allowing proactive adjustments before challenges materialize.
Reduced human error
The receipt area should allow the warehouse staff to inspect the goods before moving them to storage. The two main factors you need to consider when designing your warehouse layout are functionality and efficiency. Businesses utilise warehouses to store equipment, raw materials, finished products, packaging materials, safety stock, and machine components. Make sure that you provide adequate lighting levels based on the type function to be performed.
With these factors in mind, you’ll design a layout that promotes a safe and conducive working environment for maximum efficiency and productivity. For storage, you should consider the size, weight, and type of products to be stored when designing the storage space layout. Goods in a warehouse can be stored in shelves, pellets, or bins depending on their types, size, and weight. With a good warehouse layout design, you’ll ensure everything sits in its place to minimise damage, misplacement, and mix-ups. The shipping area is where the warehouse staff pack materials, load them into trucks and make them ready for delivery to the customer.
Label fixed areas like doors, beams, outposts, sloping floors, offices, and restrooms in your diagram to facilitate spatial planning. The type of equipment to be used in the warehouse will also significantly affect its design. Choose the right carrier service to partner with, whether domestic, regional, or international. The carrier service will help you with shipping and order fulfilment if you can’t handle it all alone.